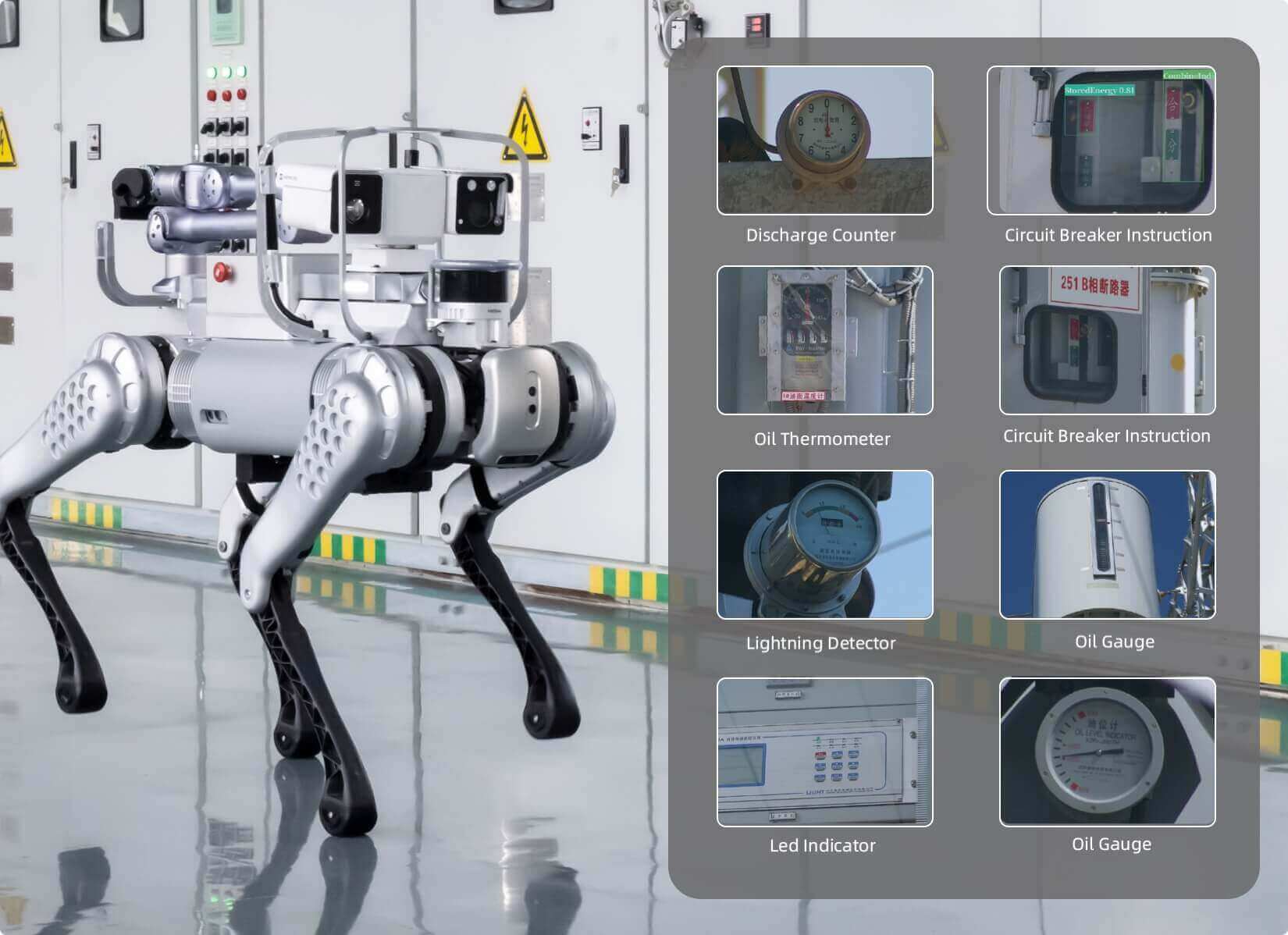
Robotics have advanced rapidly in recent years. From automation to handling tasks humans would otherwise have to do, robots can help get the job done. Our topic in this article covers quadruped robots. These robots function on four-legged structures and can maneuver in impressive ways. Specifically, power plants may utilize these four-legged bots to securely survey and inspect power plant utilities. Where human inspectors have been the primary source of these tasks, robots can reduce the risk associated with hazardous jobs.
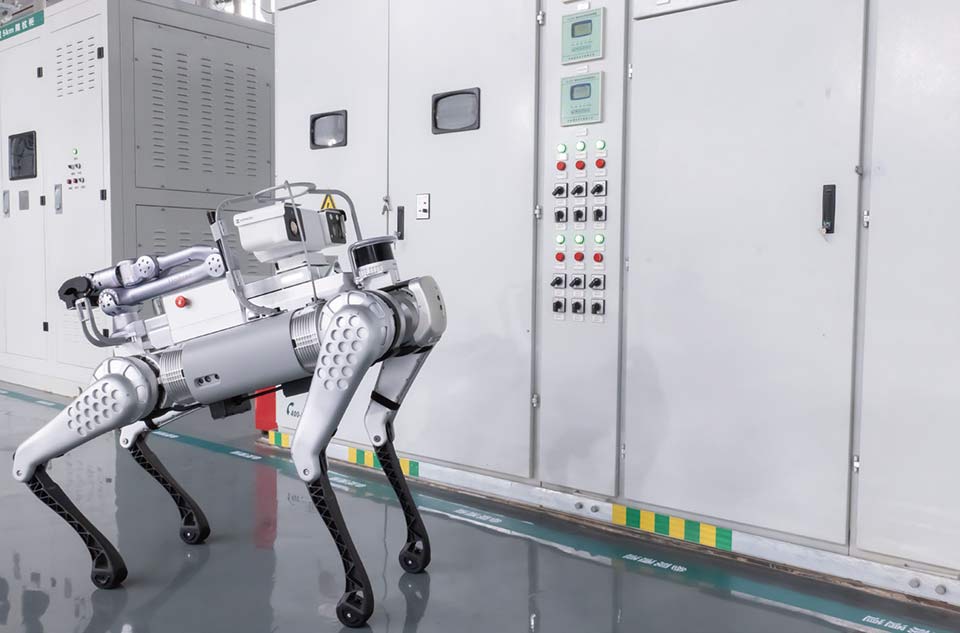
The Challenge of Power Plant Inspections
Power plants are a primary source of our planet’s energy infrastructure. However, they are also complex and hazardous environments. Routine inspections are required to maintain these facilities, not just for efficiency but also to prevent catastrophic failures of various kinds. Traditionally, human workers would conduct these inspections through confined spaces, exposure to high temperatures, and accessing elevated structures, all of which present limitations in risk, time constraints, and human ability.
Quadruped robots could address these limitations in a more efficient, safety-oriented way. Surveying and inspection tasks are some of what a robot can handle.
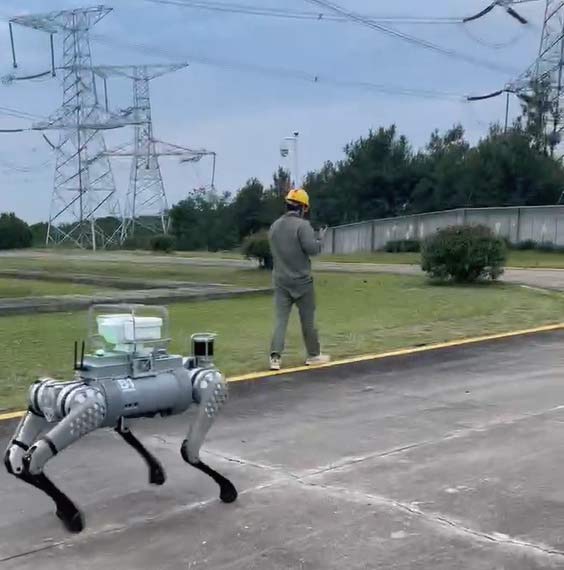
The Capabilities of Quadruped Robots
Much like your furry 4-legged friend, Quadruped robots are designed to mimic the locomotion of your beloved pet. This allows them to move over uneven terrain, navigate small, confined spaces, and climb stairs. Quadruped robots are equipped with advanced sensors and cameras, which makes them great at detecting structural abnormalities and thermal irregularities and accurately assessing the condition of equipment.
Key features of quadruped robots include:
- Mobility and Stability: Their four-legged stature keeps them balanced even on grates, stairs, and inclined platforms.
- Autonomous Navigation: These robots can program navigation. This means they can explore predetermined routes independently, allowing for less human intervention.
- Advanced Sensing Technologies: Quadruped robots have integrated sensors, such as LiDAR, ultrasonic detectors, and infrared cameras. These sensors allow the robots to gather high-quality data for analysis.
- Adaptability to Harsh Environments: These robots can withstand many challenging conditions, including extreme temperatures and high humidity. This is essential for power plant settings.
Case Study 1: Power Grid Substation in Inner Mongolia
In this project, a 220kV power grid substation in Inner Mongolia underwent comprehensive inspection using a quadruped robot B1. The inspection covered outdoor areas of 220kV and 110kV and indoor zones like the 10kV power distribution room, central control room, and relay protection room. These areas included challenging terrains such as stair ramps, mouse guards, and multiple doors.
The robot was equipped with a 3D laser radar, a dual-light PTZ camera, a robotic arm, a wireless communication module, and a charging dock to meet the project requirements. The robot autonomously navigated the inspection area, capturing critical data about the operational status of various instruments. The dual-light PTZ camera provided detailed monitoring, while the robotic arm allowed the robot to perform tasks such as closing switches.
Through real-time wireless communication, personnel in the control room could monitor the robot’s operations and receive live inspection data. This deployment fully realized autonomous, intelligent on-site inspections, significantly improving efficiency and safety.
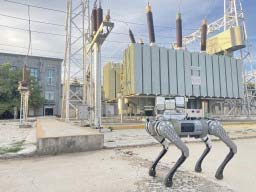
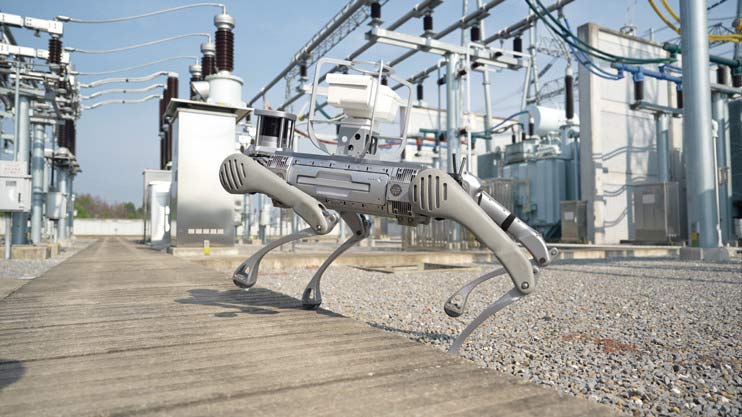
Case Study 2: Thermal Power Plant in Hebei
A thermal power plant in Hebei leveraged the capabilities of a quadruped robot B1 to inspect its 220kV booster station, boiler room, and turbine room—the project aimed to enhance operational efficiency by utilizing advanced robotics to handle high-risk and complex inspection tasks.
The robot was outfitted with a 3D laser radar, dual-light PTZ camera, acoustic imager, wireless module, and a charging dock. It autonomously navigated the plant, monitoring critical parameters such as gas concentration, partial discharges, and instrument data. The robot transmitted real-time data to the control room, allowing operators to oversee its performance and detect anomalies as they occurred.
The plant achieved a closed-loop inspection by employing autonomous navigation and intelligent diagnostic capabilities. This streamlined approach reduced operational costs, enhanced anomaly detection, and ensured the seamless monitoring of critical equipment.
Applications in Power Plant Inspection
The versatility of quadruped robots is groundbreaking for power plants. Here’s what these robots can be used for:
Structural Integrity Assessments: Robots can assess for cracks, corrosion, and any structural issues that affect the facility’s integrity.
- Thermal Imaging: Infrared cameras indicate when components overheat. It can also find leaks or insulation problems.
- Electrical Equipment Monitoring: Quadrupeds have sensors that can assess the condition of electric systems. This is useful in identifying loose connections or worn-out components.
- Hazardous Area Surveys: Robots can safely and strategically inspect inaccessible or dangerous areas for human workers.
Benefits of Quadruped Robots
The deployment of quadruped robots in power plants offers many advantages:
- Enhanced Safety: Utilizing robots minimizes the risk of accidents and injuries often present in hazardous environments.
- Increased Efficiency: These robots can conduct inspections quickly and often, saving power plants time and money.
- Cost Savings: Automating inspections reduces the cost of labor and minimizes downtime caused by equipment problems.
- Comprehensive Data Collection: High-quality data is essential for more accurate analysis. Robots can manage this, which in turn supports predictive maintenance strategies.
Future Prospects and Challenges
While the prospect of launching quadruped robots in power plant fields is promising, challenges are still expected. The initial cost to onboard this new technology is high, and the battery life still has limitations. Integrating the robots with existing technology will also be a critical yet time-consuming task.
The continuing evolution of robotic technology, combined with advancements in AI and machine learning, is expected to address the problems mentioned. Future iterations of quadruped robots will likely become more affordable, autonomous, and capable, further solidifying their role in power plant operations.
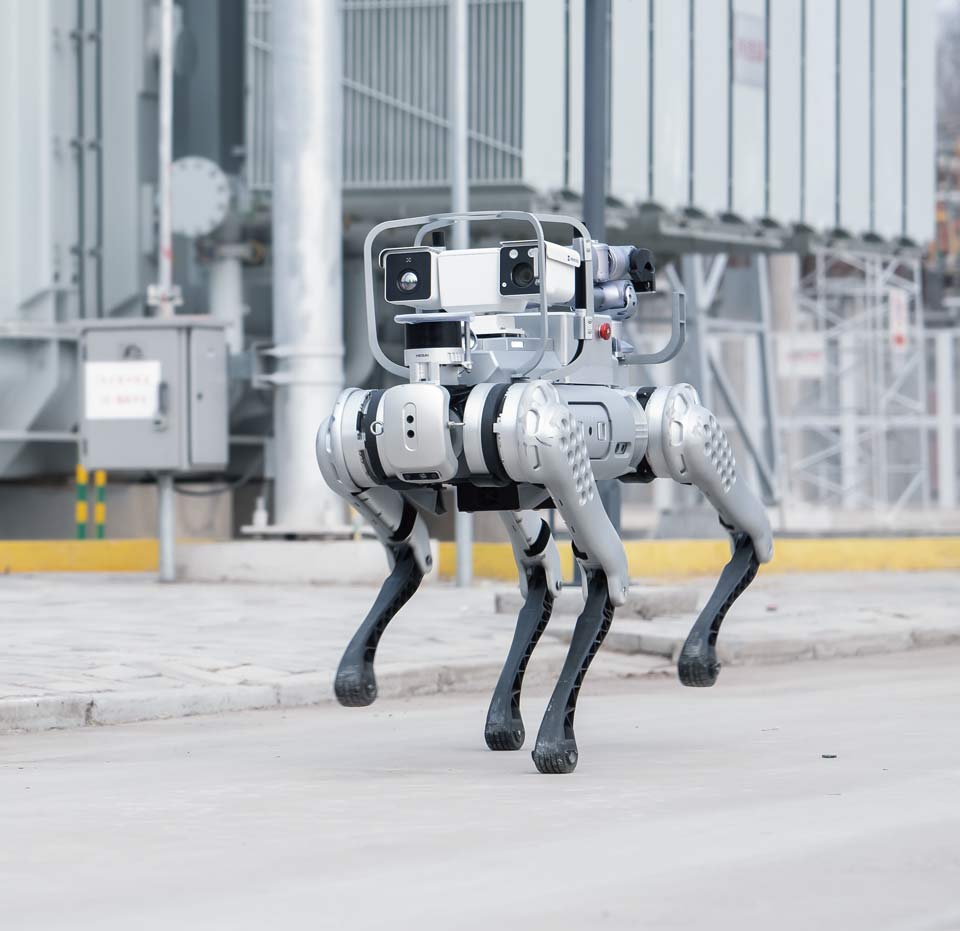
Conclusion
Quadruped robots have proven to be a significant step forward in the technological landscape. For power plants, inspections and surveying will ultimately reduce safety risks and the overall financial burden. These machines enhance safety, efficiency, and data accuracy, paving the way for a more reliable and resilient energy infrastructure. Eventually, with the ongoing advancement of quadruped robots, worldwide adoption is expected in the coming years.
This innovation ensures a seamless energy supply and creates a safer work zone for industry employees.